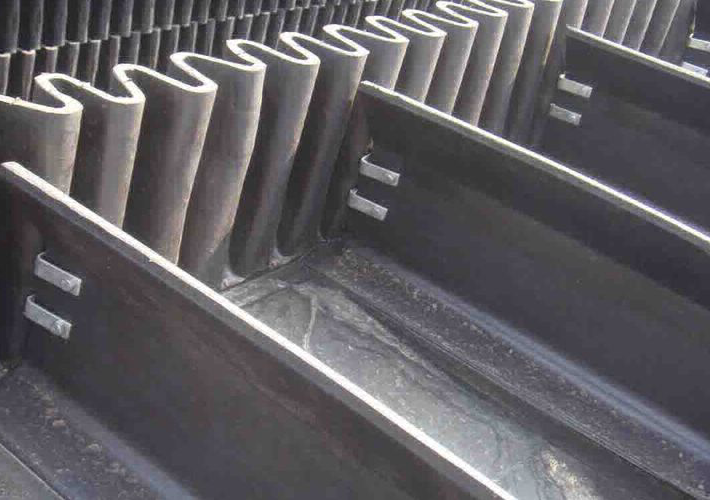
There are number of rubber manufacturing processes and each comes with one benefit or another. Understanding the manufacturing product gives you knowledge of cost and tradeoffs. The rubber industry follows these processes to manufacture different products. Here are some of the most common rubber manufacturing processes.
In the Extrusion process the unvulcanized compound is fed into the extruder. Inside the extruder it moves for dying. It is a unique manufacturing tool used to give shape to the rubber. As soon as the compound arrives at the dying stage, the right pressure pushes it to the extruder’s opening. The product will be sent for vulcanizing before it can be made useable. The rubber compound is cured and blended before the vulcanization begins. The rubber may contract or expand during the process. Also note that the length of the rubber is also impacted after vulcanization. Meanwhile, the extrusion process is suitable for producing rubber in high volumes and the cost is also affordable. The products produced during the extrusion process include gaskets, tubing, cord and profiles.
Latex dripping is process when the slim walled molds are soaked in the latex compound and later is slowly withdrawn. The thickness is increased by re-dipping it again into the latex compound. Once the dipping is over, the product is send for vulcanization. Based on the result of the dipped product different post treatments are given. The advantage of dip modling is to create complex shapes before it goes for extrusion. The outcome includes balloons, rubber gloves, tubing, grips and more.
Molding can be divided into three types:
- Compression molding: The oldest among the three and is cheaper. Here the rubber compound is made into a blank and then placed around a mold cavity to get its shape. Here the time taken for heating is low and it helps in taking a longer time for curing. The heating time can differ from three minutes to indefinite hours. This type of process is suitable for making large surface area compound with poor flow and high viscosity.
- Transfer molding is a natural and limits the compression molding. The process kick starts by loading the chamber and then distributing it into cavities. The pre-heating helps the rubber to flow into the channels. It cuts down on the curing time. The molds are expensive and complicated.
- In Injection molding the press and the injection unit are separate in terms of controls. The molds can be placed both vertically and horizontally. The extruder serves a number of presses by moving in a pre-programmed pattern. It results in a brief injection process using high pre-heating.
In Calendaring the soft material is forced in the center of the rotating rollers. Compacting the rollers and the thickness of the product, it can be determined by the distance between each cylinder, where the thickness of the product can be adjusted. The material sent through the cooling rollers is vulcanized. The process is ideal for producing films of rubber. The benefits include having a check over the thickness and the capability to make wider and thinner parts in comparison with extrusion. Here the operating cost is high when compared to others.